The Advantages of Robotic Welding Cobots
In the dynamic landscape of industrial automation, Robotic welders are constantly evolving to adapt to more and more welding processes.
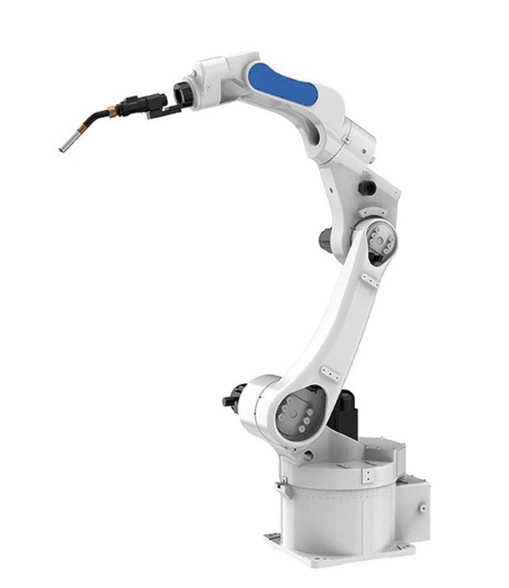
In recent years, the manufacturing industry has witnessed a transformative shift with the integration of collaborative robots, or cobots, into various processes. Robotic welding cobots, in particular, have emerged as game-changers, offering a plethora of advantages to customers in the manufacturing sector. As automation continues to redefine production processes, the adoption of robotic welding cobots is proving to be a strategic & profitable move for businesses.
Advantages of Robotic Welding Cobots
Precision & Consistency:
One of the primary advantages of robotic welding cobots is their unmatched precision and consistency. These machines are equipped with advanced sensors and vision systems that enable them to perform welding tasks with incredible accuracy. This level of precision ensures uniform welds, reducing the likelihood of defects and enhancing the overall quality of the end product. Customers can benefit from the assurance that each weld meets the exact specifications, resulting in higher quality and reliability.
Increased Productivity:
Robotic welding cobots excel in repetitive and labor-intensive tasks, leading to a significant boost in productivity. Unlike human workers, cobots do not require breaks and can operate 24/7, leading to continuous and efficient production. This increased productivity translates into faster turnaround times for customers, enabling them to meet tight deadlines and respond swiftly to market demands.
Enhanced Safety:
Collaborative robots are designed to work alongside human operators in a shared workspace. In the context of welding, this means that cobots can handle the dangerous and strenuous aspects of the welding process, allowing human workers to focus on more complex and value-added tasks. This not only improves overall safety in the workplace but also reduces the risk of injuries associated with welding activities.
Flexibility & Adaptability:
Robotic welding cobots are highly flexible and adaptable to various welding applications. Their ability to quickly switch between different tasks and adapt to changes in production requirements makes them a valuable asset for businesses with diverse product lines. Customers can benefit from the versatility of these cobots, which can be easily reprogrammed to handle different welding jobs, leading to increased operational agility.
Cost Efficiency:
While the initial investment in robotic welding cobots may seem substantial, the long-term cost savings are substantial. These machines operate with consistent efficiency, minimising material wastage and reducing the need for rework due to welding errors. Additionally, the increased productivity and decreased labor costs contribute to overall cost efficiency, making robotic welding cobots a wise investment for businesses aiming to optimise their manufacturing processes.
The integration of robotic welding cobots, including well-known brands: ABB, Kassow & Sence, into the manufacturing landscape represents a paradigm shift that brings numerous advantages to customers. From precision and consistency to increased productivity and enhanced safety, the benefits of adopting these advanced technologies are evident. As the manufacturing industry continues to evolve, businesses that embrace the advantages of robotic welding cobots are likely to gain a competitive edge, delivering high-quality products in a more efficient and cost-effective manner.
Related Products
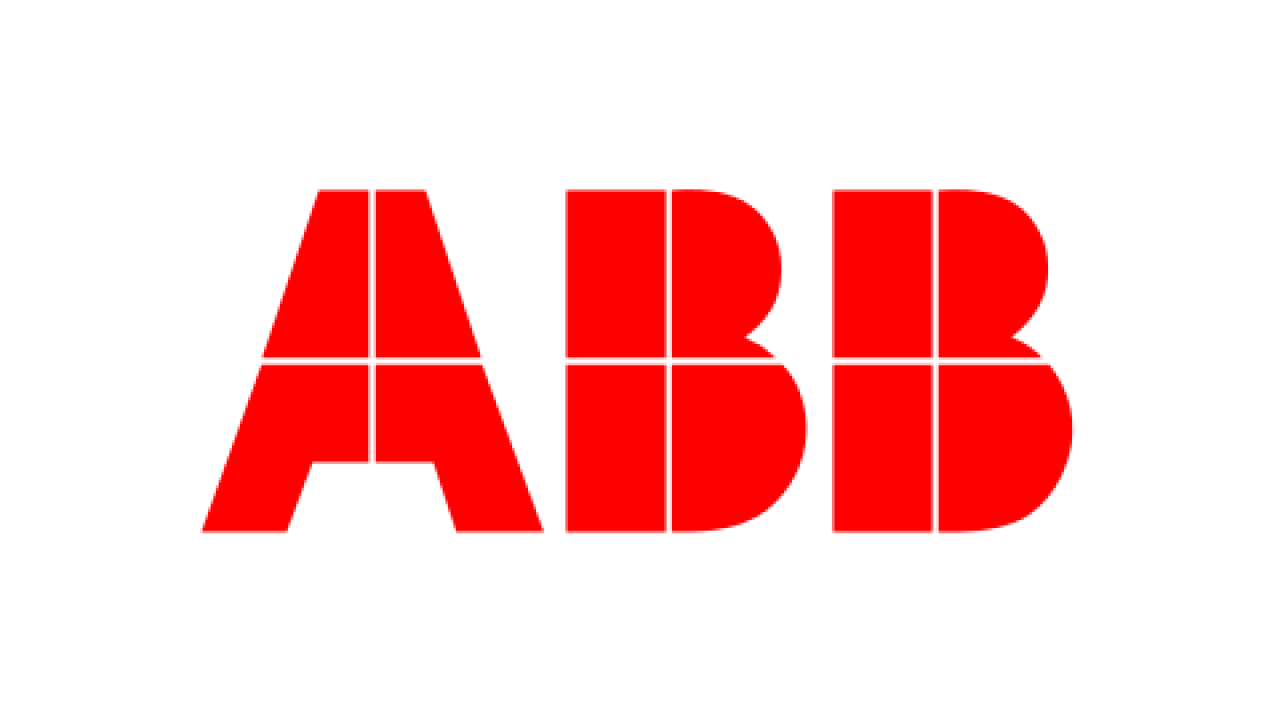
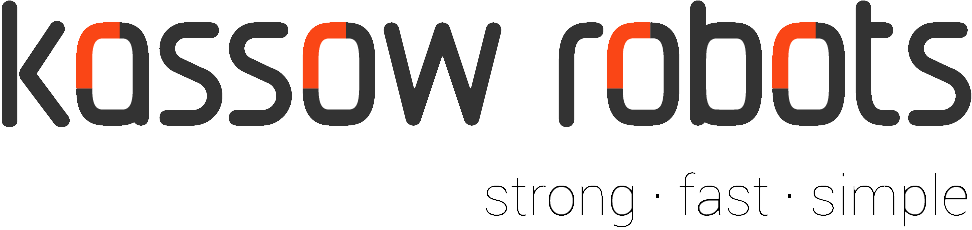
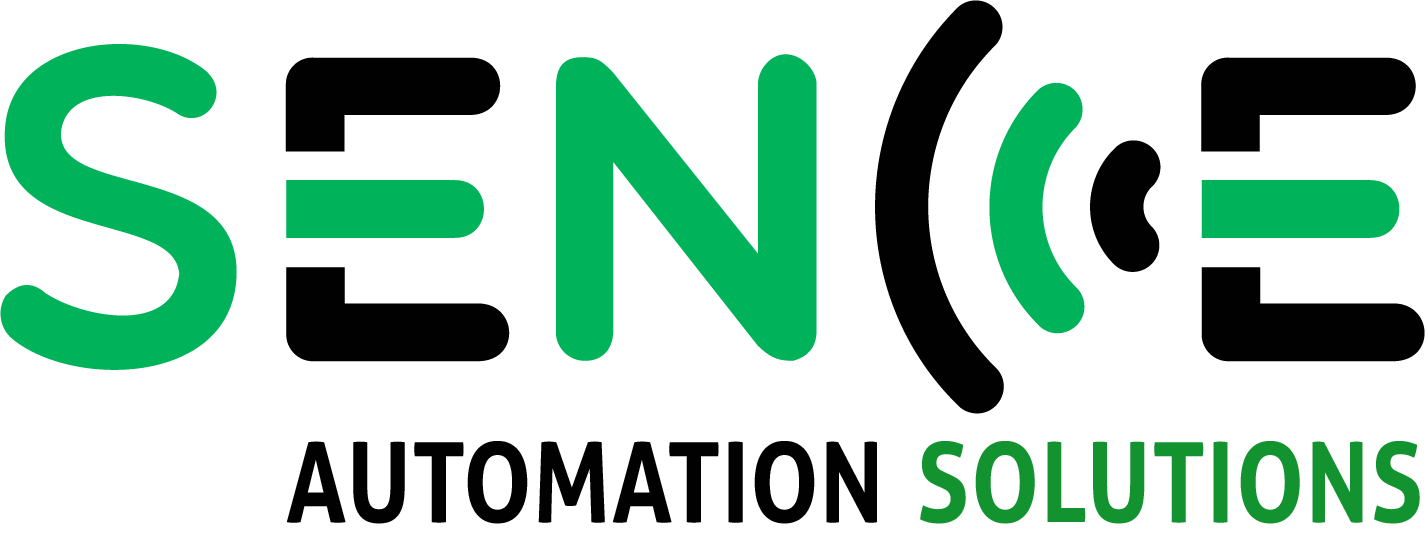