Sence Robotic Welding Cobots
In the dynamic landscape of industrial automation, Robotic Cobot Welders provide automatic tracking & correction with uninterrupted, high-quality results.

Automated Welding Workstation (Gas Shielded Arc Welding) Application Solution
Automated welding workstation (gas-shielded arc welding) is composed of the Sence E-Series collaborative robot, welding torch, welding system etc. The series collaborative robot has advantages such as integrated end force control, integrated AI vision, and high repeat positioning accuracy. In conjunction with the laser vision seam tracking system, it realises flexible dragging, automatic tracking, automatic correction, and supports long-time, uninterrupted, high-quality, and highly stable welding work.
The automated welding workstation primarily enhances cost-effectiveness in automated production fields such as auto parts, engineering machinery and metal processing. With advantages such as light guidance, flexible deployment, and high safety, it effectively solves the challenges of the shortage of skilled weldings and high labour costs in traditional welding. With automatic welding, it reduces costs and increases efficiency for customers.
Benefits & Features
Drag-and-Drop Teaching
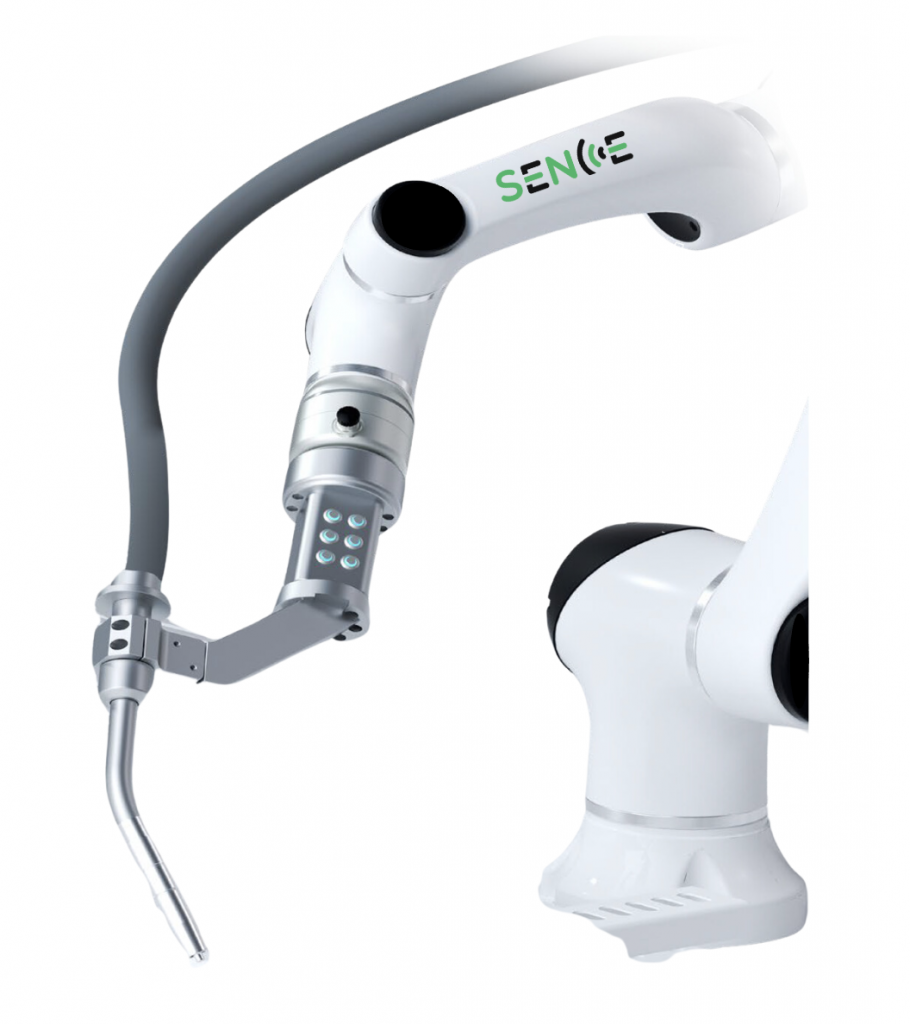
Supports integrated end force control, allowing users to drag the welding torch easily and quickly to the designated target welding point. With the end button, they can quickly establish a welding task, complete circular/ linear path selection and set up arc starting/ stopping. One drag and drop can be reused.
Laser Vision Seam Tracking
Real-time correction of welding deviation to achieve automatic seam tracking. With the laser vision seam tracking system, welding deviations are corrected in real time, ensuring that the welding gun always stays at the center of the seam during movement. This allows for automatic seam tracking, thus improving welding quality.
Arc Tracking
An arc tracking can collaborate with the robot to obtain the relative position of the welding gun and the groove by collecting and processing arc signals, correcting any deviations in the robot’s planned path.
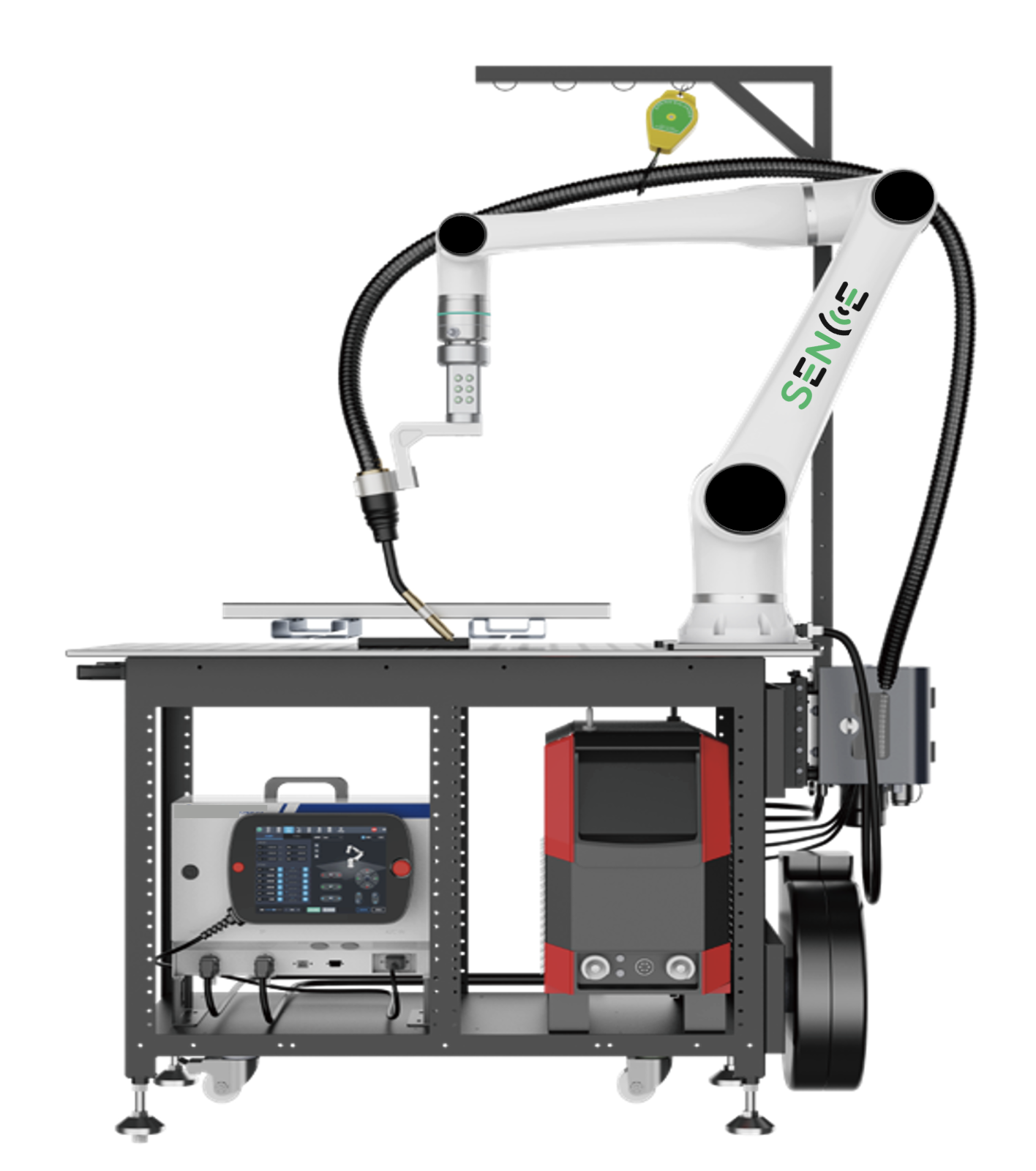
Easy-to-Use Welding Plug-in
Provides an easy-to-install, easy-to-use welding plug-in. The user-friendly interface meets visual and graphical operation needs, enables benign human-machine interaction, and improves production efficiency.
The automated welding workstation (gas shielded arc welding) can rapidly operate through point setting, drag teaching, and intelligent remote sensing. The welding technique package can flexibly configure current, voltage, welding speed, welding posture etc. meeting users needs for quickly setting up various welding applications.
Multiple control techniques for high-quality welding
Short-circuit transition control process with special energy control, pulse energy regulation of the melt-drop transition control process, and the synergistic process based on variable wire feed speed pulsed energy control process, which is extremely suitable for the consistent high-quality welding of carbon steel, stainless steel, aluminum allows etc. uniformly high-quality welding.
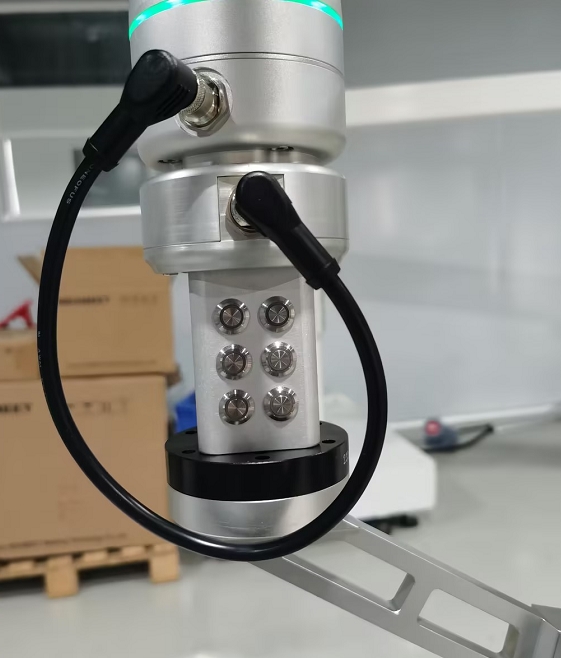
Graphical programming, quick mastery within 10 Minutes
The welding process package integrates a wealth of parameters to meet the needs of the welding process. Straight or circular welding can be carried out with simple commands, select and define linear, circular, and zigzag paths by moving the robot arm to the points of your choice and locking them with buttons on the flange to make welding as easy as using a mobile phone.
Flexible drag teaching, improved work efficiency
The collaborative robot integrates end force control, possesses excellent precision and accuracy, realises smoother, more efficient drag teaching abilities. A one-time teaching for repeated use can automate and continually perform welding tasks, significantly improving work efficiency.
Multiple Safety protections ensure safe production
Uses an electromagnetic brake mode in the event of a sudden power failure or emergency stop during operation. It can be held directly without falling which effectively increases operational safety.
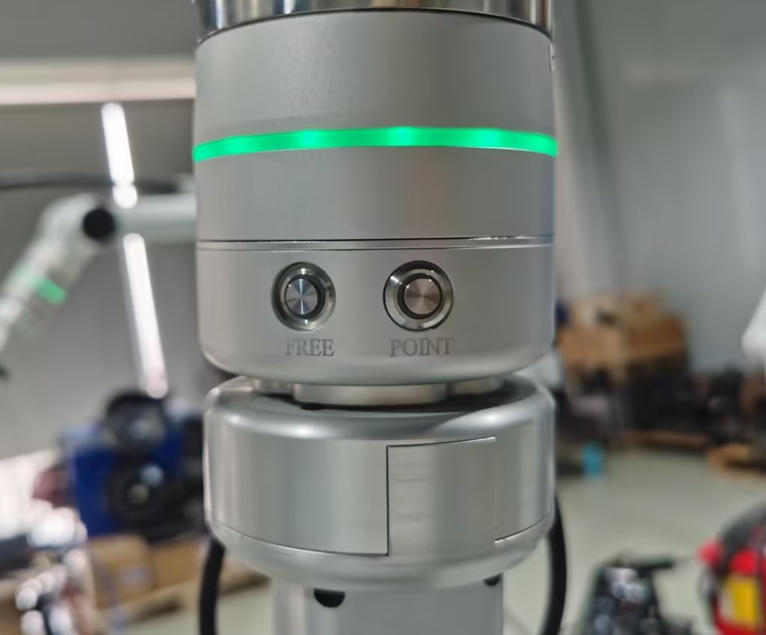
User-friendly UI interface, for stress-free work.
Optimises and upgrades the system UI interface based on actual user application scenarios, allowing the robot to serve users better.
Industry Applications
- Metal Working
- Automobile Components
- Shipbuilding
- Kitchen & Bathroom Industry
Resources
PDF, 10MB
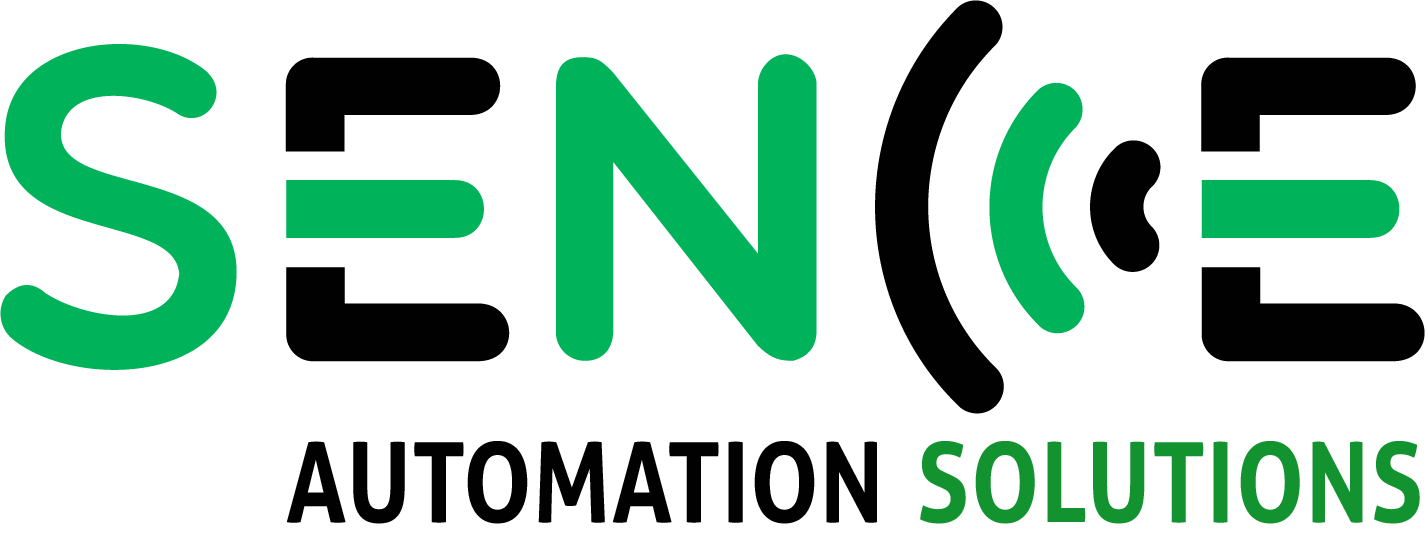